Prueba de pulverización salina en vidrio laminado
La adopción del vidrio laminado como material estructural en arquitectura está creciendo prácticamente de manera exponencial, dado que arquitectos, diseñadores e ingenieros están empezando a tomar conciencia del potencial añadido aportado por las interláminas modernas.
Tradicionalmente adoptados por motivos estéticos, los materiales tales como las interláminas de PVB y de ionómero, han incrementado significativamente sus aplicaciones para vidrio, especialmente donde resulta necesario que el soporte sea mínimo o la seguridad post- rotura constituye una fuente de preocupación.
No obstante, con esta creciente apuesta por lo nuevo, y aplicaciones más exigentes, es necesario llevar a cabo pruebas adicionales para propiciar tranquilidad respecto a que los paneles de acristalamiento estructural pueden resistir las mismas condiciones medioambientales que los elementos estructurales que les rodean o que les soportan. Por lo tanto, tiene sentido, si los componentes de metal están sujetos a rigurosos ensayos, los elementos estructurales lo estén también.
Una vía de ensayos está midiendo el efecto adverso de las condiciones medioambientales, especialmente en aplicaciones costeras con una gran carga de sal. La prueba de pulverización salina es uno de los ensayos de corrosión más extendidos y asentados en el tiempo. La prueba ASTM B117 de exposición a la pulverización salina (niebla) fue la primera prueba de pulverización salina en ser reconocida oficialmente, siendo publicada originalmente en 1939. Otras pruebas, incluida la 2604-05 de la AAMA, Asociación Americana de Fabricantes Arquitectónicos (por sus siglas en inglés), requieren que todos los componentes arquitectónicos metálicos con revestimiento demuestren una resistencia a la corrosión al ser sometidos a una prueba de pulverización salina a lo largo de 3.000 horas de exposición. Además, las Directrices-CWCT del Centro de Tecnología para Ventanas y Revestimientos en el Reino Unido recomiendan el uso de materiales a prueba de agua salada a una distancia de hasta 50 millas de la línea de costa.
Si tuviéramos que realizar esta prueba al vidrio por sí solo, no observaríamos efectos adversos; al ser el vidrio un material relativamente inerte. No obstante, puede no ser el caso de las interláminas, sobre todo al ser utilizadas en paneles laminados de canto expuesto.
Rajan Govind, Director de BES Façade Consultants, India, tiene un argumento muy contundente al respecto. “Cuando hablamos sobre barandas de vidrio como un sistema completo en un balcón, no
Sólo nos referimos al metal sino al vidrio también, ambos están sometidos a exactamente las mismas condiciones. Si los paneles de vidrio desarrollan algún defecto visual en tales aplicaciones, ello representaría una terrible experiencia para el propietario de cualquier condominio de lujo en Mumbai o donde sea. ¿Entonces, no tiene sentido someter al vidrio también a ensayos?”
Con esto en mente, como parte de sus continúas actividades enfocadas al desarrollo del producto, los ingenieros de Trosifol, sometieron recientemente a una rigurosa prueba de pulverización salina a una variedad de muestras de vidrio laminado en el laboratorio TÜV SÜD en Singapur.
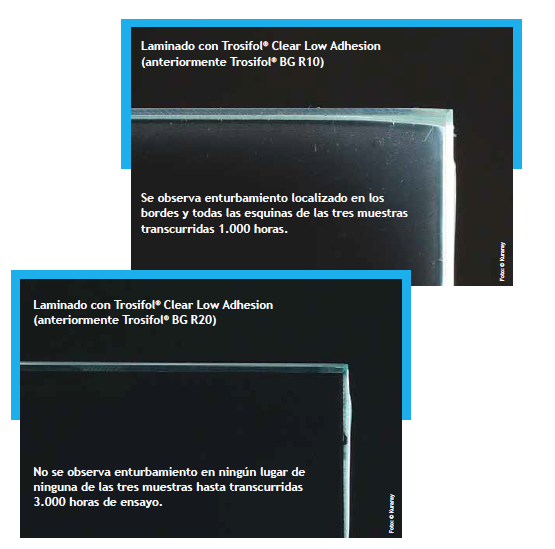
Los paneles de 150 x 100 mm (5,9 x 3,9 pulgadas) están integrados por dos paneles de vidrio recocido de 3 mm (0,12 pulgadas) con una interlámina de 1,52 mm (60 mil) entre ellos. Se sometieron a ensayo interláminas de Trosifol® Clear Low Adhesion, Trosifol®UltraClear High Adhesion, Trosifol® Extra Stiff y SentryGlas®.
Se fabricaron cuatro paneles de vidrio con bordes esmerilados para cada tipo de muestra en los laboratorios de Trosifol, en Troisdorf, Alemania. Se seleccionaron tres muestras al azar para cada tipo de muestra para el ensayo conservando la cuarta muestra como referencia.
Todos los paneles de vidrio se expusieron a unas condiciones medioambientales que emulaban niebla salina de acuerdo con el siguiente método y condiciones de ensayo. Cada panel de vidrio fue entonces evaluado visualmente en intervalos de 500 horas en busca de cualquier defecto de borde, como por ej. delaminación, enturbiamiento, burbujas, etc.
Condiciones de ensayo
Concentración de Solución Salina: 5±1 % w/w NaCl
G.E de Condensado: 1,029 – 1,033
pH de Condensado: 6,5-6,9
Volumen de Condensado: 1,0-2,0 ml/hr/80 cm2
Temperatura cámara de pruebas : 35± 2°C
Posición del panel de vidrio: Inclinación 15° de la vertical
Tiempo de Exposición : 3,000 hrs.
En el primer intervalo de 500 horas, ninguna de las muestras dio señales de ningún efecto nocivo fruto de la pulverización salina. Tras 1.000 horas, la muestra de Trosifol® Clear Low Adhesion empezó a dar señales de enturbiamiento en los bordes mientras que la de Trosifol® Extra Stiff únicamente empezó a verse afectada en las esquinas transcurridas 2.500 horas. Las muestras fabricadas con interláminas de Trosifol®UltraClear High Adhesion y SentryGlas® no presentaron ningún defecto. El ensayo de pulverización salina – especialmente en el caso de paneles con bordes expuestos – es increíblemente corrosivo, pero Trosifol sostiene la creencia de que es importante evaluar la idoneidad de los productos. Para verlo con perspectiva, no está demás mencionar, que las cuatro interláminas pasan los requisitos de la prueba ISO 12543, que incluyen pruebas de calor húmedo durante dos semanas y una prueba de horneado a 100 °C.
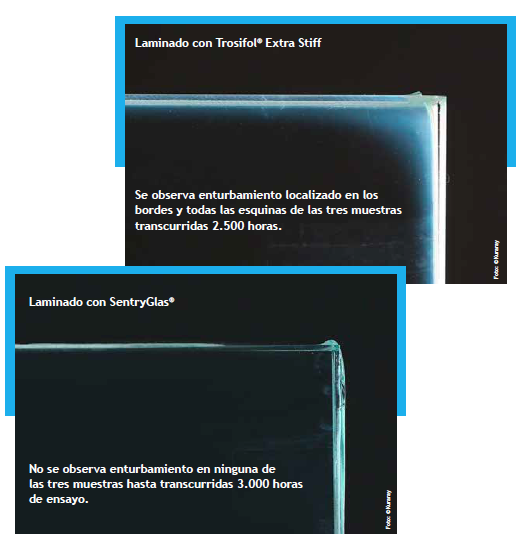
Como resultado del régimen de pruebas, Trosifol puede recomendar la interlámina de PVB Trosifol® UltraClear High Adhesion para aplicaciones de vidrio laminado con bordes expuestos al medioambiente, debido a su elevada estabilidad de borde. Para aplicaciones estructurales, tales como barandas, fachadas fijadas por puntos, marquesinas, etc., con bordes expuestos en zonas costeras y, de manera crítica, donde la resistencia post-rotura es también vital, se recomienda la interlámina SentryGlas® debido a su elevada estabilidad de borde y rigidez.
Rajan Govind viene a sumar sus pensamientos: “He visto mucha delaminación, particularmente en aplicaciones de barandas donde los bordes están expuestos, así que este tipo de pruebas resultan vitales para garantizar las características a largo plazo de los paneles laminados en términos de estética y funcionalidad. Las aplicaciones del vidrio laminado están aumentando en la industria de las fachadas, auxiliadas en parte por los mandatos y legislación local. Hemos estando utilizando estos materiales durante 10 años y el futuro se muestra esperanzador para una variedad de diferentes aplicaciones. Desde mi perspectiva, el siguiente paso será alguna forma de garantía
basada no solo en el material de la interlámina, sino también en las capacidades y seguridad de los laminadores que la aplican. Según mi lógica, esto abrirá la base de aplicaciones de un modo significativo.”
A medida que el vidrio empieza a ver cómo van en aumento sus ratios de utilización como material estructural en aumento, tiene sentido que sea sometido al mismo régimen de pruebas al que lo son las estructural que lo rodean. Puede que estos ensayos resulten algo duros para los laminados, pero resulta vital el garantizar que pueden comportarse igual en las mismas condiciones – ofreciendo las mismas capacidades estructurales y en términos estéticos para las que fueron recomendadas originalmente. El ensayo continuo y desarrollo del producto es habitual en Trosifol, dado que continuamente busca y ofrece a sus clientes incluso más tranquilidad llegado el momento de elegir y aplicar las interláminas líderes a nivel mundial de PVB e ionómero.